Category 

ArticlesMetal ContainersAmber GlassCosmetics and BeautyThe Fun StuffSustainable PackagingPlastic BottlesBottlesGlass JarsFood and BeveragePlasticsGlass BottlesEnvironmental ImpactInfographicsGuidesClosuresTrends and TechnologyContainer UpdatesVideosOils and AromasHealth and PharmaceuticalCustomer StoriesPackaging DesignMason Jars
Blog
Infographic
Guide
The silk screen printing process outlined in just 7 steps

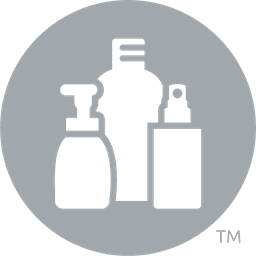
Unknown Author
Added January 1, 2018
5 minute read
Silk Screen printing is the most common and widely used form of decoration in the industry.
Silk screening is very effective for one and two color designs. We can print 3 color designs, but such prints become very difficult and more expensive. Also, the loss or scrap factor increases significantly. If you are interested in multiple colors, consider a label (for larger quantities) or a heat transfer process.
Silk screen printing is a fairly involved process, with many steps.
- Create a screen. A screen is a piece of silk stretched tightly over a wooden or metal frame. A screen must be stretched to a specified degree of tension. When a screen is too loose, the silk is allowed to shift slightly, causing a blurry image. If the screen is too tight, it may easily tear during the printing process, or peel away from the wood or metal frame.
- Once a screen is stretched, the screen is coated with an emulsion (similar to emulsion used in a photographic process). This emulsion is light sensitive.
- Next, a film positive (a picture of the desired print on a clear plastic sheet) is taped to the emulsion-covered screen, and the screen is placed in a lighted area. At Container & Packaging Supply, we use a metal light box which controls the amount and type of light to which the screen is exposed. Similar to photography, the emulsion is exposed to light, which hardens the emulsion in all uncovered areas. Because the film positive is covering parts of the emulsion, those parts or not hardened and may be washed out.
- Following the exposure time, a screen is washed, and all emulsion covered by the film positive washes out, leaving the desired picture or image clearly burned into the screen.
- Set up the print machine. With the screen ready, a semiautomatic machine must be set up to print a specific container with the specific image already burned into our screen. Gears must be used which match the diameter and size of the container to be printed. Squeegees that fit the dimensions of the container must also be found and a myriad of other adjustments must be made to a machine to allow the container to be printed correctly. The screen is also placed on the machine.
- Printing. Silk screen printing involves pushing ink through the holes in silk in the shape of the image previously burned into the screen. In the case of bottle printing, where the print surface is round, we have to rotate the bottle at the same speed we move the screen across the bottle. By carefully timing both the movement of the screen and the bottle, a clear image is left on the container.
- Drying. Once printed, the bottle must be dried. We send our printed containers through large dryers set at specific temperatures for specified time periods. This process allows the ink to cure and adhere to the container. Solvents within the ink dissolve during this time, leaving a hardened ink on the bottle.
While overly simplified, hopefully this description provides a basic understanding of how silk screen printing works.
