
Behind the Scenes: How Glass Bottles Are Manufactured
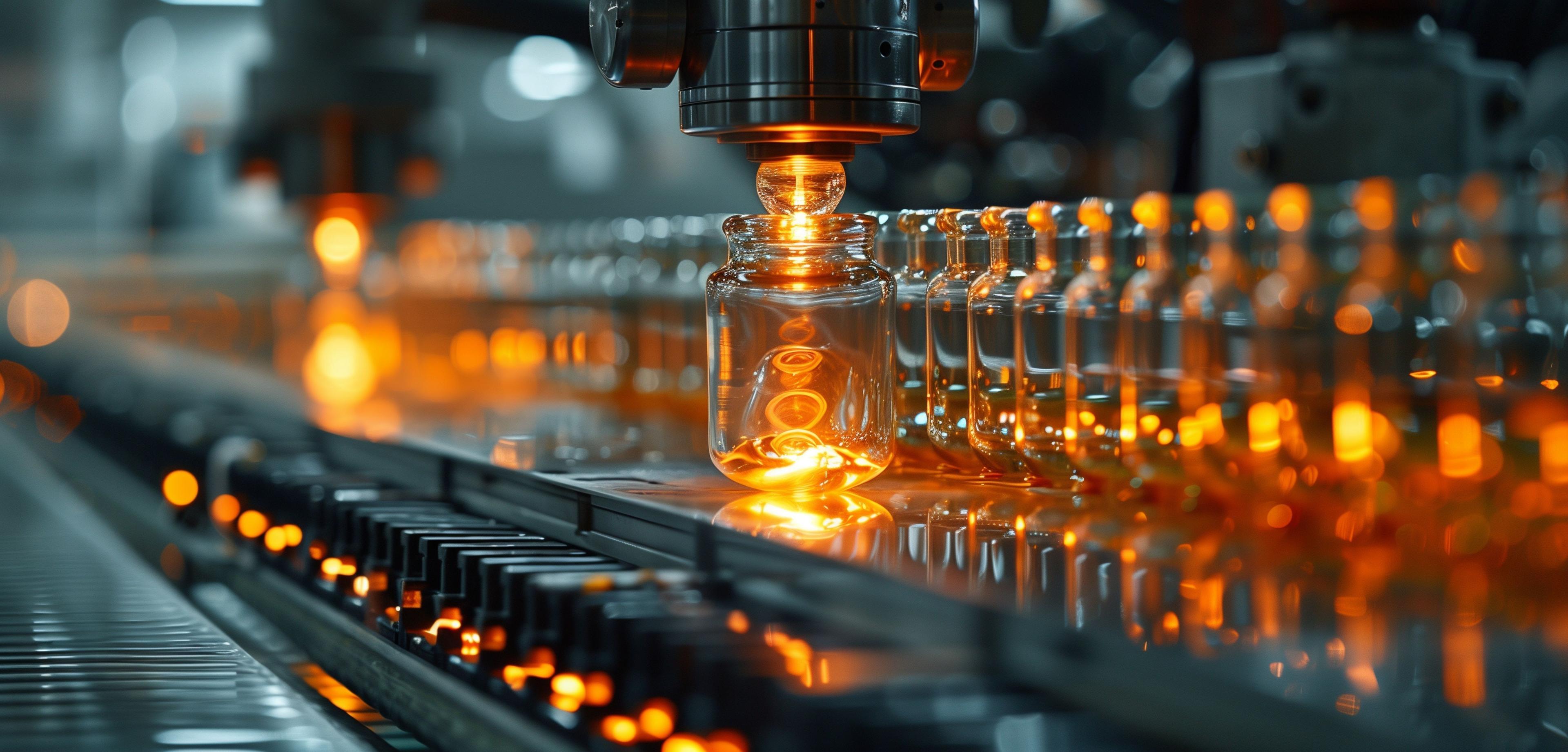
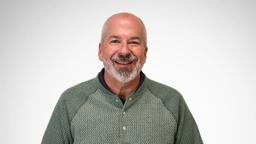
Glass bottles are everywhere—from the soda in your fridge to the sparkling water on your desk. But have you ever wondered how these everyday containers are made? Spoiler alert: it’s a mix of fiery temperatures, incredible precision, and centuries-old craftsmanship. Let’s peek behind the curtain and uncover the fascinating process of glass bottle manufacturing.
A Brief History of Glass Manufacturing
Before we dive into today’s cutting-edge processes, let’s tip our hats to history. Glassmaking dates back to around 2000 BCE in ancient Mesopotamia. Early artisans crafted glass vessels by hand, blowing molten glass into shapes with nothing more than a pipe and lung power. Thankfully, we’ve come a long way since then—although the essence of the process remains remarkably similar.
The Raw Ingredients: What Makes a Glass Bottle?
At its core, glass is surprisingly simple. It’s primarily made from three ingredients:
- Silica (Sand): The main ingredient, making up about 70% of the mix.
- Soda Ash: Reduces the melting temperature, saving energy during production.
- Limestone: Adds durability to the final product.
Sometimes, manufacturers add recycled glass (cullet), which melts at a lower temperature and reduces waste. In fact, most modern glass bottles contain 20-80% recycled material—good for the planet and production costs.
Step 1: Melting the Ingredients
Creating glass starts with extreme heat—think 2,700°F (1,500°C). The raw materials are fed into a furnace, where they melt into a molten, honey-like consistency. These furnaces operate 24/7 because cooling them down and reheating them is about as practical as turning off the sun for the night.
Fun fact: The molten glass glows orange, and it’s mesmerizing to watch.
Step 2: Shaping the Glass
Now for the real magic: turning that molten goo into a perfectly shaped bottle. This is where technology meets artistry.
- Gobs of Glass: The molten glass is cut into chunks called gobs. Each gob is precisely measured to ensure consistency in bottle size and weight.
- Molding: These gobs are dropped into molds, where compressed air blows them into the desired shape. This process is called the blow-and-blow or press-and-blow method, depending on the bottle design.
- Cooling: Once shaped, the bottles are cooled gradually in an annealing oven. This controlled cooling prevents stress fractures and ensures the glass is strong and durable.
Step 3: Quality Control
Not all glass bottles make the cut. Advanced machines inspect each bottle for flaws, like bubbles, cracks, or uneven thickness. Imperfect bottles are recycled back into the furnace, ensuring zero waste in the process.
The Final Touches
Depending on the bottle’s purpose, additional steps might include:
- Coloring: Additives can give glass a specific hue, like green for wine bottles or amber for beer bottles.
- Labeling: Some bottles are printed with labels directly on the glass, while others are fitted with paper or adhesive labels after production.
- Coating: To improve durability and reduce friction, bottles are often coated with a thin protective layer.
Why Glass Bottles Are a Sustainable Choice
Glass isn’t just beautiful and versatile—it’s also one of the most eco-friendly packaging options out there. Here’s why:
- Infinite Recyclability: Unlike plastics that degrade after recycling, glass can be melted and remade indefinitely without losing quality.
- No Chemical Leaching: Glass doesn’t leach harmful chemicals, making it a safer choice for food and beverages.
- Energy Efficiency: Using recycled glass in production reduces energy consumption significantly.
By choosing glass, companies can reduce their environmental footprint while offering premium, reusable packaging.
Real-World Examples of Glass Bottle Innovation
1. Lightweight Glass Bottles
Some companies are experimenting with lightweight glass bottles that use up to 40% less material. This innovation reduces shipping costs and environmental impact while maintaining strength and durability.
2. Custom Shapes and Designs
From perfume bottles shaped like jewels to whiskey bottles embossed with intricate designs, glass offers unparalleled customization.
3. Smart Packaging
Imagine a wine bottle with an embedded NFC chip that tells you the wine’s origin and ideal pairing. Smart packaging is taking glass bottles to the next level.
Conclusion
Glass bottle manufacturing is a fascinating blend of ancient techniques and modern innovation. From raw materials to the finished product, every step in the process is designed for precision, efficiency, and sustainability.
So, the next time you sip from a glass bottle, take a moment to appreciate the journey it’s been on. And if you’re looking for premium glass packaging for your business, Container & Packaging has you covered—whether you need classic designs or something totally custom.
